Porosity in Welding: Identifying Common Issues and Implementing Finest Practices for Prevention
Porosity in welding is a prevalent concern that commonly goes unnoticed up until it triggers significant problems with the integrity of welds. This usual issue can jeopardize the strength and durability of bonded frameworks, positioning safety dangers and bring about pricey rework. By comprehending the source of porosity and carrying out effective avoidance techniques, welders can significantly boost the high quality and integrity of their welds. In this discussion, we will certainly explore the essential aspects adding to porosity development, examine its harmful effects on weld performance, and discuss the most effective techniques that can be adopted to minimize porosity event in welding processes.
Usual Root Causes Of Porosity
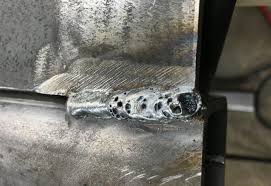
Making use of filthy or wet filler products can introduce impurities right into the weld, contributing to porosity concerns. To alleviate these usual causes of porosity, extensive cleaning of base metals, correct shielding gas option, and adherence to ideal welding parameters are essential techniques in achieving high-grade, porosity-free welds.
Impact of Porosity on Weld Quality

The presence of porosity in welding can substantially endanger the architectural integrity and mechanical residential properties of bonded joints. Porosity creates spaces within the weld steel, weakening its general stamina and load-bearing ability.
Welds with high porosity degrees have a tendency to display lower impact strength and lowered capacity to flaw plastically before fracturing. Porosity can hinder the weld's ability to successfully transmit forces, leading to early weld failing and potential safety hazards in essential frameworks.
Ideal Practices for Porosity Avoidance
To improve the structural integrity and top quality of bonded joints, what details actions can be executed to reduce the incident of porosity during the welding process? Utilizing the appropriate welding method for the details product being welded, such as adjusting the welding angle and weapon placement, can additionally prevent porosity. Normal assessment of welds and immediate removal of any kind of issues recognized during the welding procedure are crucial methods to avoid porosity and produce high-quality welds.
Significance of Proper Welding Techniques
Carrying out appropriate welding techniques is extremely important in making sure the architectural integrity and top quality of welded joints, building upon the structure of reliable porosity prevention actions. Welding strategies straight affect the general strength and durability of the bonded structure. One vital aspect of appropriate welding methods is preserving the appropriate warm input. Excessive warm can bring about enhanced porosity due to the entrapment of gases in the weld swimming pool. Conversely, inadequate warm may result in insufficient blend, creating possible powerlessness in the joint. Additionally, using the appropriate welding criteria, such as voltage, present, and travel rate, is essential for accomplishing sound welds with marginal porosity.
Furthermore, the selection of welding procedure, whether it be MIG, TIG, or stick welding, need to straighten with the details requirements of the project to ensure ideal results. Appropriate cleansing and preparation of the base steel, along with selecting the appropriate filler product, that site are also vital elements of proficient welding strategies. By sticking to Resources these finest methods, welders can decrease the danger of porosity development and generate high-quality, structurally audio welds.
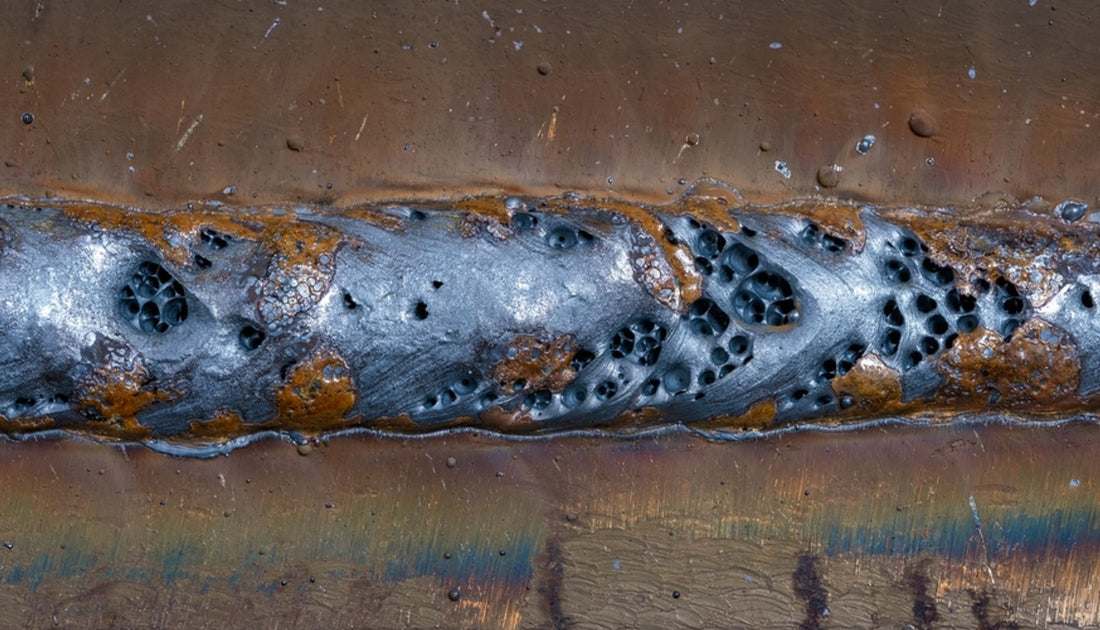
Evaluating and High Quality Control Measures
Examining procedures are important to find and prevent porosity in welding, making certain the strength and sturdiness of the final item. Non-destructive screening methods such as ultrasonic screening, radiographic testing, and aesthetic assessment are typically used to determine possible problems like porosity.
Post-weld inspections, on the other hand, assess the last weld for any kind of problems, including porosity, and validate that it meets specified standards. Carrying out a thorough quality control plan that includes comprehensive screening treatments and evaluations is paramount to decreasing porosity concerns and guaranteeing the general high quality of bonded joints.
Verdict
Finally, porosity in welding can be a typical problem that impacts the high quality of welds. By determining the common sources of porosity and implementing navigate here ideal methods for avoidance, such as proper welding methods and testing actions, welders can make sure excellent quality and trusted welds. It is important to prioritize avoidance methods to lessen the occurrence of porosity and maintain the stability of bonded frameworks.